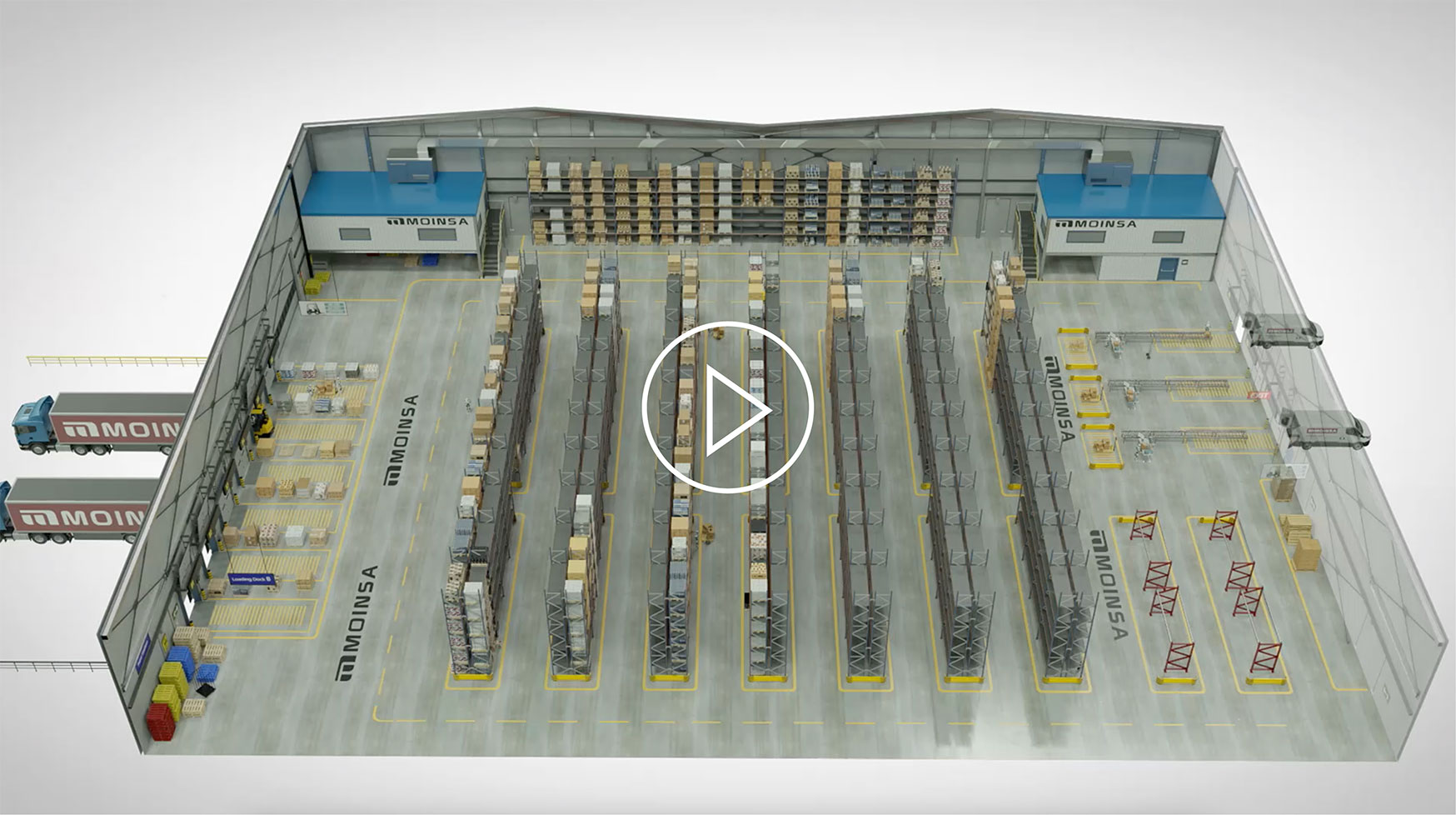



1. UNLOADING AND RECEIVING GOODS
2. STORAGE
3. ORDER PREPARATION
4. ORDER SHIPPING
5. ORDER DELIVERY
Unloading and receiving goods
Implementing a WMS brings the following advantages:
If you want to learn more about terminals click here.
If you want to learn more about our WMS click here.
Implementing a WMS brings the following advantages:
- Quick verification of delivery notes.
- Immediate registration of received items.
- Traceability of delivery date and time by the supplier.
If you want to learn more about terminals click here.
If you want to learn more about our WMS click here.

Unloading and receiving goods
During downloading and reception, the condition, quantity, and
preparation of the merchandise are verified. Its entry is recorded,
and it is optimally located to minimize time and errors.
During downloading and reception, the condition, quantity, and
preparation of the merchandise are verified. Its entry is recorded,
and it is optimally located to minimize time and errors.
Storage
After receiving the goods, we proceed with restocking.
The advantages of following this process, as shown in the infographic, include:
If you want to learn more about terminals click here.
If you want to learn more about our WMS click here.
After receiving the goods, we proceed with restocking.
The advantages of following this process, as shown in the infographic, include:
- Dynamic space allocation, maximizing storage utilization.
- Strategic placement of references to optimize subsequent picking (A, B, C).
- Error-free placement of goods.
If you want to learn more about terminals click here.
If you want to learn more about our WMS click here.

Storage
In this phase, the operator scans the goods, and the WMS indicates their location.
A second scan confirms the operation and updates inventory in real time.
In this phase, the operator scans the goods, and the WMS indicates their location.
A second scan confirms the operation and updates inventory in real time.
Order preparation
Productivity increases in the picking process due to:
If you want to learn more about terminals click here.
If you want to learn more about our WMS click here.
Productivity increases in the picking process due to:
- Automatic direction of operators to locations, optimizing route planning.
- Automatic recording of picked items in the database, eliminating paper
use and manual data entry - Error-free process.
- Simplification of the subsequent shipping process.
If you want to learn more about terminals click here.
If you want to learn more about our WMS click here.

Order preparation
During order preparation, the system informs the operator what to pick and where.
Using a handheld terminal, the operator scans the products and places them on a
pallet for shipment.
During order preparation, the system informs the operator what to pick and where.
Using a handheld terminal, the operator scans the products and places them on a
pallet for shipment.
Order shipping
Productivity increases due to:
If you want to learn more about terminals click here.
If you want to learn more about our WMS click here.
Productivity increases due to:
- Printing of barcode labels for destinations.
- Lower error rates, as references are automatically grouped.
- Confirmation of each stage the goods go through.
If you want to learn more about terminals click here.
If you want to learn more about our WMS click here.

Order shipping
During shipping, the operator receives the order, prints automatic labels,
and loads it onto the correct truck for distribution.
During shipping, the operator receives the order, prints automatic labels,
and loads it onto the correct truck for distribution.
Order delivery
This process confirms receipt and updates information in real time,
improving traceability and logistics efficiency.
If you want to learn more about terminals click here.
If you want to learn more about our WMS click here.
This process confirms receipt and updates information in real time,
improving traceability and logistics efficiency.
- Real-time confirmation.
- Improved traceability.
- Error reduction.
- Greater transparency for the customer.
If you want to learn more about terminals click here.
If you want to learn more about our WMS click here.

Order delivery
Upon arrival at the destination, the operator scans the label, updating the WMS
and confirming delivery.
Upon arrival at the destination, the operator scans the label, updating the WMS
and confirming delivery.
Increase your profitability starting now
Get in touch with the Moinsa team for any questions you may have about our solution.
We will be happy to assist you and provide all the information you need with the utmost transparency and prompt communication.